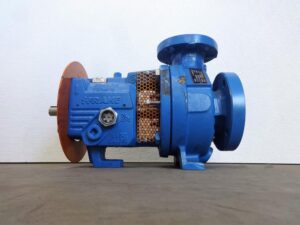
ZPEX Coating: A Game-Changer for Iodine Removal from Corrosive Brine
Introduction: In the iodine extraction process from brine, corrosive environments can pose a significant challenge for centrifugal pumps. However, the
ZPEX™ is a revolutionary coating system offering complete corrosion protection without over-machining or masking.Thin enough for threads and sealing.
Strong enough to replace stainless steel.
ZPEX is a revolutionary coating system that’s half as thick as a dollar bill—making it perfect for tight clearances inside your pumps, valves, and fittings.
Get the industry’s most comprehensive corrosion, abrasion, and efficiency protection without having to over-machine or mask your parts. Just coat, re-assemble, and run as usual.
ZPEX has increased the lifespan of multiple manifold systems and valves that were historically failing prematurely due to constant immersion in saltwater and H₂S, saving us time and money on repairs and replacements.
Ecoat.us has solved multiple failure issues. ZPEX has increased the lifespan of multiple manifold systems and valves that were historically failing prematurely due to constant immersion in HCl and salt water, saving us time and money on repairs and replacements. We routinely recommend our customers to Ecoat.us for their customer service and ZPEX coating system.
Save up to 70% by switching from exotic metal alloys to coated carbon without sacrificing strength or reliability.
Survive long-term in chemically rich & mechanically harsh environments (Like uncoated stainless can’t)
Reduce friction for faster, smoother fluid flow and less energy consumption
ZPEX offers a powerful solution to prevent galling of threads, ensuring enhanced performance and longevity.
Protect 100% of your components (even hard-to-reach recesses and threads) against wear and corrosion
Eliminate chipping, peeling, and creep-back of corrosion underneath the coating
ZPEX starts by electro-depositing an eighth-generation hybrid polyepoxide coating over a surface that has been meticulously pretreated with zirconium oxide. This initial step creates a chemical-resistant base coat that forms an electro-molecular bond with the substrate. The result is a superior bond that goes beyond the surface, preventing chipping, peeling, and the insidious creep-back of corrosion underneath the coating.
High-density polyepoxide coatings are renowned for their exceptional adhesion and chemical resistance. But they often fall short in environments where abrasion and solids are present . That’s where ZPEX truly shines, taking protective coatings to the next level by incorporating a fluoropolymer layer over the electro-deposited epoxy base coat. This ingenious combination fuses the best qualities of both technologies into a single, uniform layer of protection that’ll keep your parts performing for years to come.’
ZPEX is a factory applied, proprietary coating system that in most cases can replace stainless steel and other exotic metallurgy.
The ZPEX coating system consists of an electro-deposited epoxy primer (e-coat), cross linked with a fluoropolymer topcoat. The e-coat primer, or Cathodikote (our trademark brand of e-coat), is applied when the part is completely submerged in a series of process tanks tanks with multiple stages for cleaning, rinsing, pre-treatment, and Ecoat. The Ecoat is an electro-deposited epoxy, which is very thin and very chemical resistant, with second to none adhesion to the substrate.
The second part of the process is the fluoropolymer topcoat which crosslinks with the e-coat primer. This coat is selectively spray applied to the fluid/potential corrosion areas of the components. The end result is very even, thin, extremely chemical resistant and slick coating that can be applied to threads, balls, seats, and any other low tolerance areas of equipment within valves, pumps, and manifolds.
Acetone
Acetic Acid
Acetates (ALL)
Amines (ALL)
Ammonia
Ammonium Hydroxide
Amino Acids
Benzene
Borax
Boric Acid
Butyl Alcohol
Butyl Cellosolve
Butyric Acid
Calcium Chloride
Calcium Hypochlorite
Carbon Tetrachloride
Cetyl Alcohol
Chlorides (ALL)
Chlorine Gas
Chromic Acid (NR)
Citric Acid
Creosol
Diesel Fuel
Diethanolamine
Ethyl Acetate
Ethyl Alcohol
Ethyl Ether
Fructose
Gasoline
Glucose
Glycol
Glycol Ether
H2CO3
Hydrochloric Acid
Hydrochloric Acid
Hydrogen Peroxide 5%
Hydrogen Sulfide
Hydrazine
Hydroxylamine
lodine
Isobutyl Alcohol
Isopropyl Alcohol
Kerosene
Lactic Acid
Lauryl Acid
Magnesium
Maleic Acid
Menthol
Methanol
Methylene Chloride
Methyl Ethyl Ketone
Methyl Isobutyl Ketone
Mustard Gas
Naphthol
Ozone
Perchloric Acid
Phenol 85%
Phosgene
Phenolphthalein
Phosphoric Acid
Potassium Chloride
Potassium Hydroxide
Propyl Alcohol
Propylene Glycol
Salicylic Acid
Salt Water
Sodium Bisulfite
Sodium Chloride
Sodium Hypochlorite 5%
Sodium Hydroxide <10%
Sodium Sulfate
Stearic Acid
Sucrose
Sulfuric Acid 25-28%
Sulfates (ALL)
Sulfates (ALL)
Sulfates (ALL)
Starch
Toluene
Triethanolamine
Xylene
Introduction: In the iodine extraction process from brine, corrosive environments can pose a significant challenge for centrifugal pumps. However, the
Introduction: ZPEX coating has proven its mettle in various applications, including brine environments. This post highlights the success stories of
Introduction: In industries where corrosive agents, such as brine, are commonly encountered, finding corrosion-resistant materials and coatings is crucial. This
The top coat for the Zpex Coating System is a fluoropolymer, wet spray application that is
selectively applied to the ‘working’ surfaces of the part. Followed by another final bake cycle that
crosslinks the primer and topcoat together, creating a very dense, very thin coating system.
Zpex is typically applied at around 1.3-2 mils thick, about half the thickness of a dollar bill.
In comparison to those types of coatings, Zpex is certainly very thin. Most powder systems are
applied at anywhere from 5-10 mils thick, and most 3 part epoxy systems at around 10-14 mils
thick. Both far too thick to be internally applied to valve components that include seat pockets
and threads.
No, thats actually one of the key advantages of using Zpex. Because the coating is so thin, no
additional over machining or masking is necessary. Which means no additional cost for machine
time, and no creating of an edge, which, when masking is necessary, is the first place corrosion is
going to attack.
Zpex can be applied to any surface that is conductive. We most typically apply Zpex to carbon steel or cast iron in replacement of stainless steels, however, somewhat often, we will apply Zpex to stainless steel also
We’ll make sure they don’t turn into liabilities with ZPEX.